Dalcos coil-fed punching machines: raw material savings, parametric programming, and high-speed production

Coil-fed punching technology has been a specialty of the Dallan group for thirty years. Nowadays, they are even more efficient, versatile, and productive.
If you produce using sheet-fed punching machines
Dalcos coil-fed punching allows you to produce while saving up to 20% of material and with a much higher productivity, since the loading and unloading times for the sheets is eliminated!
Furthermore, with automatic parametric programming, you can forget about programming using DXF and traditional post-processing software, and program your product families with varying lengths and widths using simple Excel reports!
If you already produce using a coil-fed system, but with a press and dies
Dalcos coil-fed punching allows you to eliminate expensive blanking dies, as it uses commercial tools for thick turret punching machines. There’s no need for expensive modifications when your customer requires a modification to the product, all you need to do is reprogram the position of the hole and the notch! Consequently, you have maximum flexibility, and moreover, using the same coil you can also create different products one after the other, with different lengths and punching without ever having to stop or retool the machine!
Maximize the use of the material
In traditional sheet-fed punching, up to 20% of material is regularly wasted, because it’s not possible to get an exact number of pieces from the sheet metal. Even with the most efficient nesting, it’s often necessary to leave a connecting skeleton between the pieces, which then need to be detached automatically or manually. That is a huge waste.
Instead, imagine being able to insert your products on a continuous coil, where the pieces are made one after the other, then sheared, practically without wasting any material.
That is precisely the advantage that Dalcos coil-fed punching provides!
In production, all you need to do is look at the bins full of scrap material and check the annual cost of sheet metal to immediately realize how much of a saving 20% of all punched sheets generates.
Not to mention that, if it doesn’t exist, there’s no need to manage and dispose of the scrap!
It is an opportunity for savings (and therefore for the creation of positive cash flow), which no company can afford to overlook nowadays. To check whether your production and the size of your production batches would allow you to benefit from these enormous advantages, please contact our specialists for advice!
Automatic production and extensive processing autonomy
Another huge obvious advantage is, automatic and continuous production. There is no need for large, complex automatic warehouses. Production starts with sheet metal coils, which are compact and take up less warehouse space, they’re easy to handle and there’s no risk of damaging the material, unlike traditional sheets!
A coil, once installed on the decoiler, contains thousands of meters of sheeting, which is processed continuously without waiting times, since the processed product automatically loads the next one.
Once the operator has loaded the coil, they can leave the machine to function on its own.
Indeed, we have customer companies that run four Dallan punching systems with a single operator!
Production is also able to continue unattended during the night. Lots of Dalcos customers load a coil at the end of the shift and come back to find a pallet of finished pieces the next morning. Almost like a dream.
Furthermore, the products are stacked in a simple, continuous manner and, considering the cost of a decoiler and stacking system, it becomes immediately apparent how much cheaper a coil-fed punching system is compared to sheet-fed systems, also and above all in terms of system costs!
99% of the time, the pieces produced are already detached and come out finished and without micro joints, ready for bending operations.
Dalcos coil-fed punching machines are also designed to be positioned in line with Dallan roll forming machines or even with existing roll forming machines from other manufacturers.
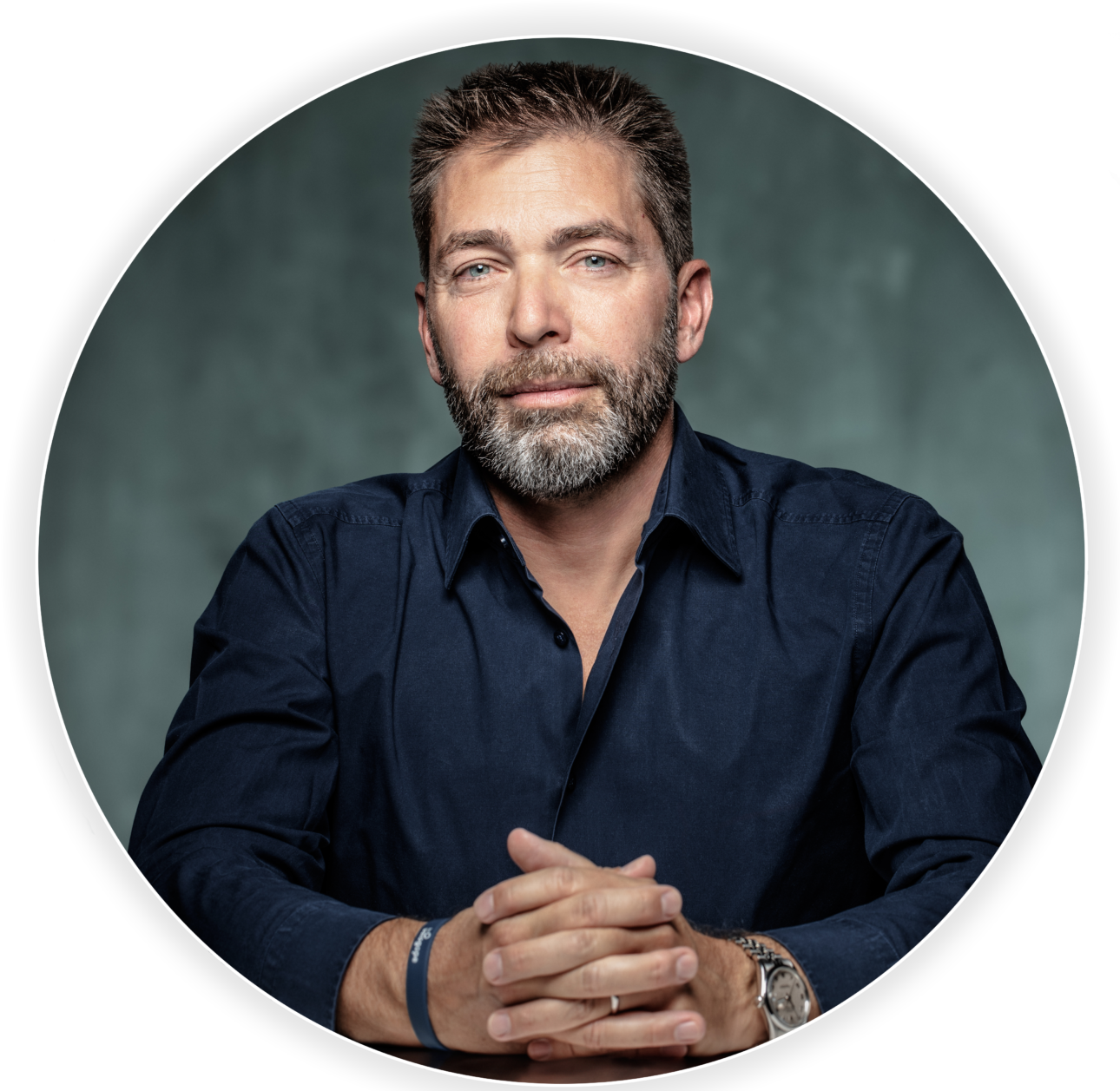
Andrea Dallan
CEO – Dallan Spa