The efficient coil-fed Punching
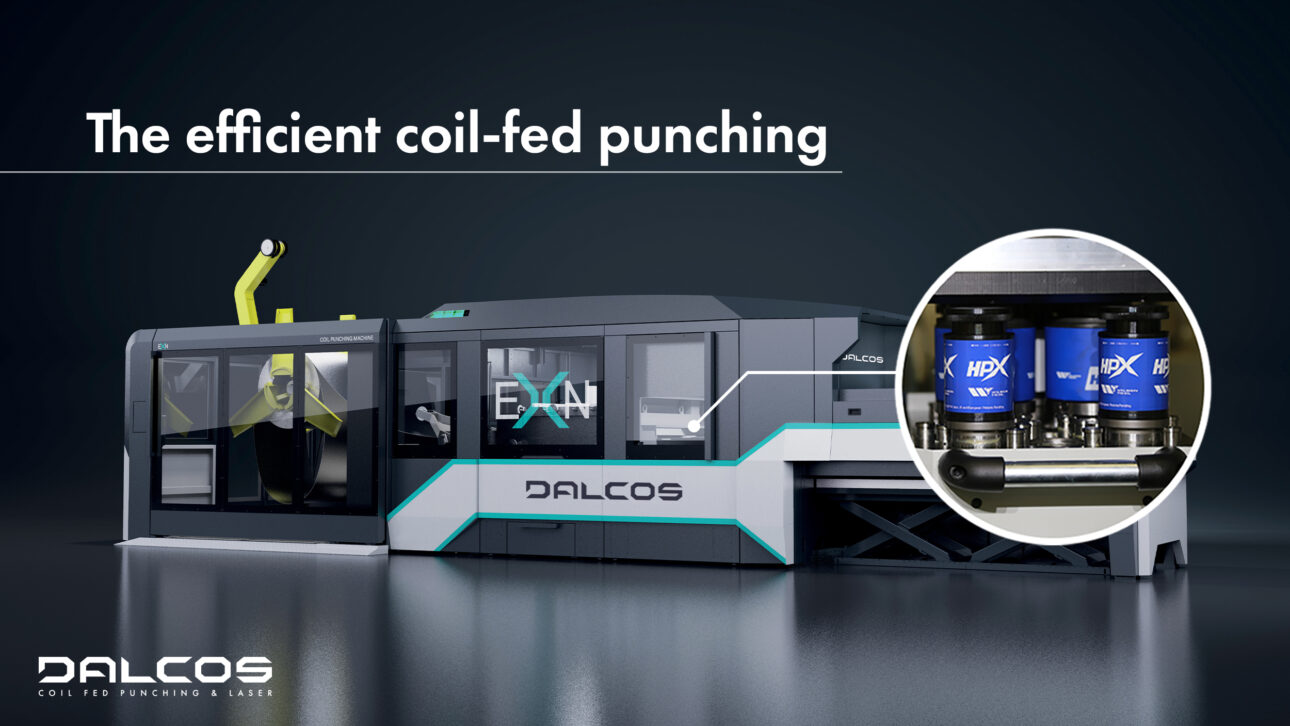
Dalcos Coil Punching Machines – Saving Raw Materials, Parametric Programming, and High Production Speed
Punching technology from coils has been a specialty of the Dallan group for thirty years: today, they are even more efficient, versatile, and productive.
If You’re Producing with Sheet Punching Machines
Dalcos coil punching allows you to save up to 20% of material and achieve much higher productivity as it eliminates the time for loading and unloading the sheet!
Moreover, with automatic parametric programming, you can forget about programming through DXF and traditional post-processing software, and program your product families variable in length and width starting from simple Excel spreadsheets!
If You’re Already Producing from Coils, but with Press and Dies
Dalcos coil punching enables you to eliminate the costly dies for cutting, as it uses commercial turret punch press tools: expensive modifications are no longer needed when your customer requests a product change, just reprogram the hole position and notching! This gives you maximum flexibility, and also from the same coil, you can produce different products one after another, with different lengths and punches without ever having to stop or retool the machine!
Maximizing Material Use
In traditional sheet punching, up to 20% of the material is regularly wasted because it is not possible to get an exact number of pieces from the sheet of metal: even with the best nesting, it is often necessary to leave a connecting skeleton between the pieces, which then have to be detached automatically or manually. This is a huge waste.
Imagine instead being able to insert your products into a continuous strip, where the pieces are made one after another and sheared, practically without waste of material.
This is exactly the advantage that Dalcos coil punching offers!
In production, it is enough to observe the bins full of scrap material and check the annual cost of sheet metal to immediately understand how much savings are generated by the 20% of all the punched sheets.
Not to mention that the scrap, if not there, does not even have to be managed and disposed of!
This is a savings opportunity (and therefore of creating positive cash flow), which no company today can afford to overlook: to check if your production and the size of your production lots allow you to benefit from these great advantages, contact our specialists for a consultation!
Automatic Production and Great Work Autonomy
Another great advantage is clearly the automatic and continuous production: there is no need for large and complex automatic warehouses. Production starts from coils of sheet metal, which are compact and take up less space in storage, are easy to handle, and without risks of damaging the material as can happen with sheets!
Once the coil is installed on the unwinding spindle, it contains thousands of meters of strip, which are processed continuously without waiting times, as the processed product automatically loads the next one.
Once the coil is loaded, the operator can leave the machine to work on its own.
Consider that we have client companies, which with a single operator manage even four Dalcos punching plants!
Production is able to continue unattended even during the night, and many Dallan clients load a coil at the end of the shift, to find the pallet of finished pieces the next morning. Almost a dream.
Moreover, the products are stacked in a simple and continuous way, and considering the cost of the unwinding spindle and stacking system, it is immediately clear how much more convenient the coil punching system is compared to sheet systems, also and above all in terms of plant cost!
The produced pieces are in 99% of cases already detached and come out finished and without micro-joints, ready for bending operations.
Dalcos coil punching machines are also ready to be lined up with Dalcos profile makers, or with existing profile makers from other manufacturers.
To discover more about our punching lines, contact us.
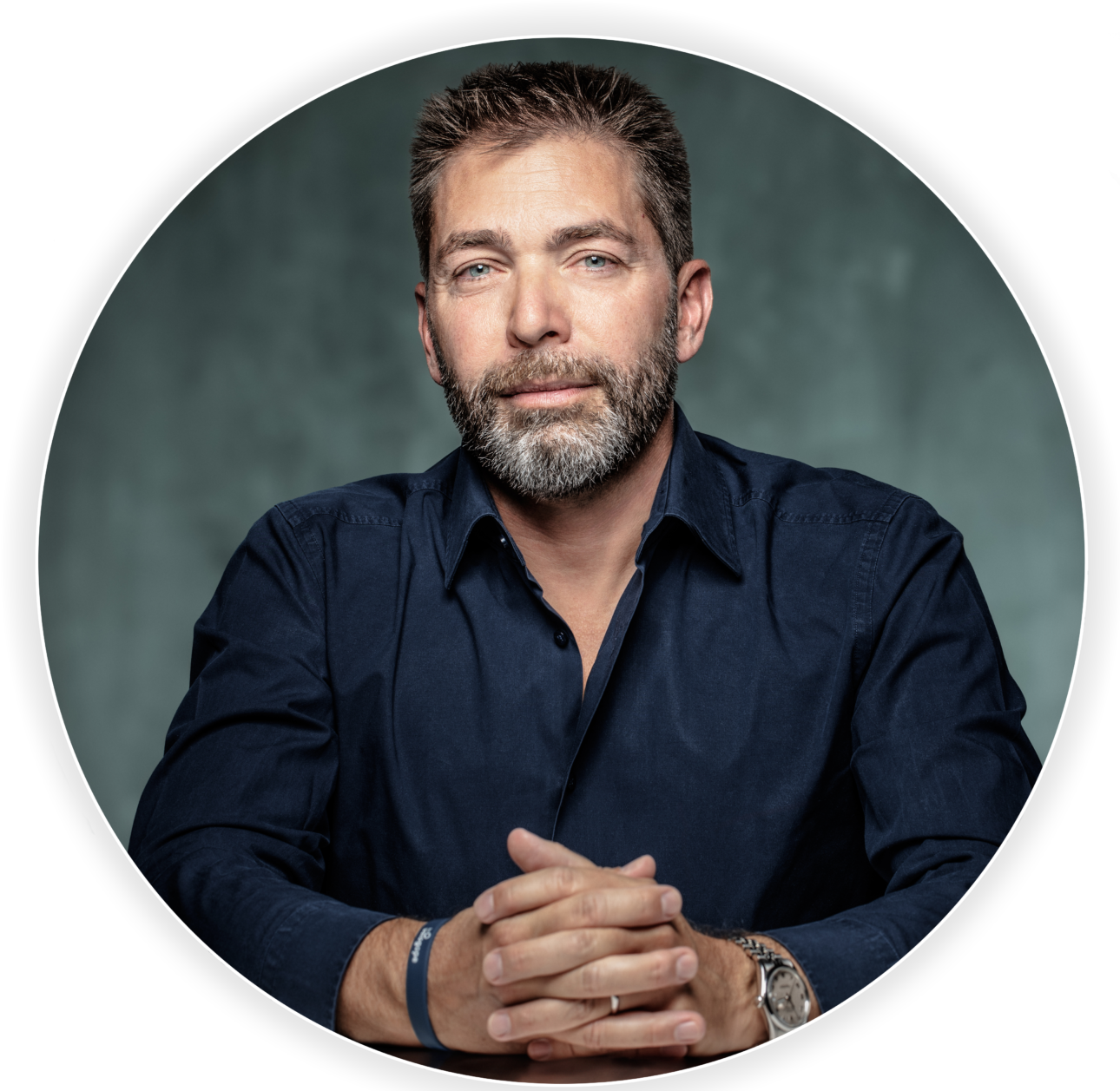
Andrea Dallan
CEO – Dallan Spa