Punzonado a partir de bobina – Sostenibilidad y Flujo de Caja de los procesos Eficientes
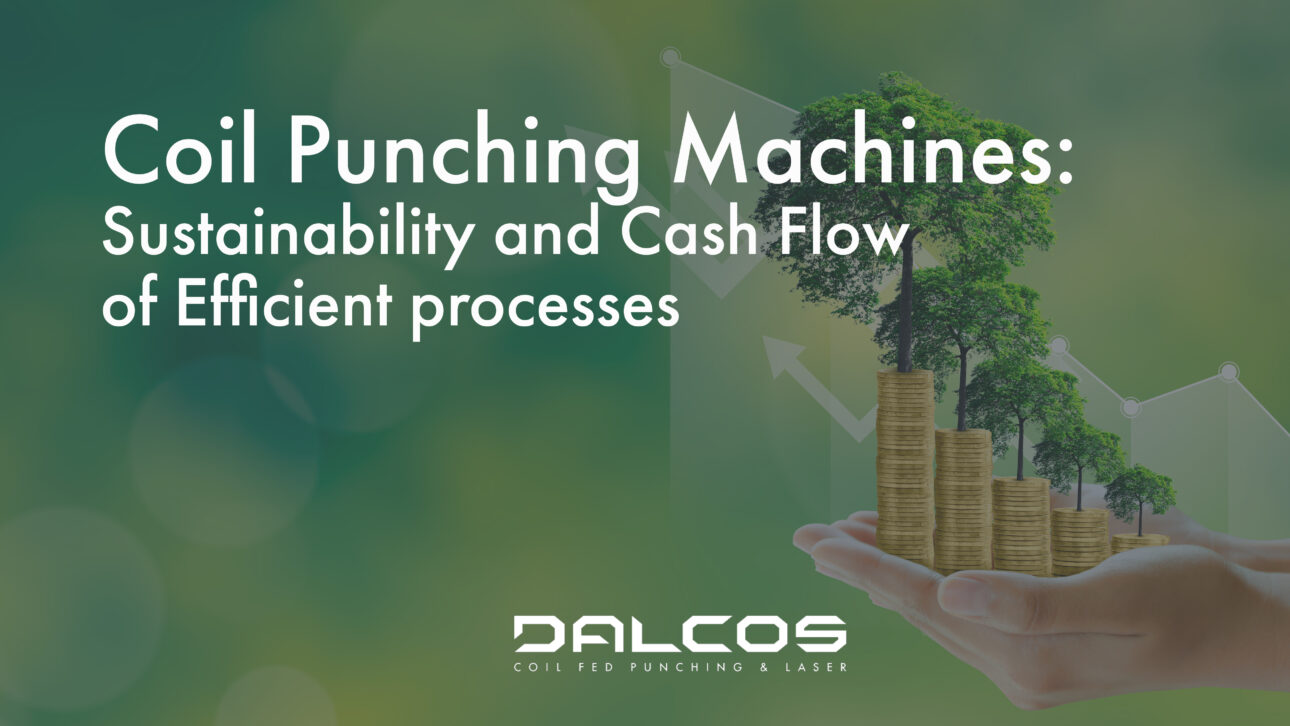
Resolver el problema de la Eficiencia de los procesos tiene dos efectos positivos.
En primer lugar, introducir el trabajo de bobina en el proceso –como hemos visto– supone un ahorro en materia prima que puede superar el veinte por ciento produciendo la misma cantidad de producto. Esto se traduce en un aumento de los márgenes y en un flujo de caja positivo inmediatamente disponible para la empresa.
Los resultados pueden variar en función del sector y de la aplicación. En todo caso, se trata de materiales que el empresario y la empresa ya no tienen que comprar, que ni siquiera hay que gestionar ni eliminar sus desechos. Todo el proceso resulta mucho más rentable y el resultado positivo se refleja de inmediato en los márgenes.
Además, al adquirir menos materia prima, la empresa logra automáticamente que el proceso sea más sostenible, ¡porque esa materia prima ya no se tiene que producir por adelantado!
La eficiencia energética constituye otro elemento importante en la economía de cada ciclo de producción.
En un sistema moderno de producción moderno, el consumo de una perfiladora es relativamente bajo. Gracias al sistema Combi, las líneas pueden estar dotadas de varios motores pequeños accionados por inversor (en lugar de un solo motor especial grande).
La energía empleada es exactamente la que requiere el proceso de moldeado, incluida la fricción en los órganos de transmisión.
En otros tiempos, las máquinas rápidas con corte volante tenían un gran problema: la disipación de energía en las resistencias de frenado. En efecto, el grupo de corte aceleraba y desaceleraba todo el tiempo, lo que suponía un gran derroche de energía.
En la actualidad, con los modernos circuitos que utilizamos, podemos acumular la energía en el frenado y restituirla en el proceso de perfilado y en el siguiente ciclo de aceleración, recuperándola en gran parte y poniéndola a disposición de la instalación y de los otros procesos. Además, casi todos los traslados eléctricos están controlados por inversores digitales: ¡comparado con las soluciones tradicionales, se puede recuperar hasta un 47 por ciento de energía!
Otro problema del balance energético de una máquina es la presencia de actuadores hidráulicos.
La hidráulica tiene todavía una función muy importante en las máquinas. En efecto, todavía no existen actuadores servo-eléctricos con capacidad para generar tanta fuerza en tan poco espacio.
Durante los primeros años, en las punzonadoras de bobina, solo usábamos cilindros hidráulicos como actuadores para los punzones. Las máquinas y las exigencias de los clientes seguían aumentando, igual que el tamaño de las centrales hidráulicas que se aplicaban a las máquinas.
La central hidráulica transporta el aceite a presión y lo distribuye por toda la línea, ocasionando pérdidas de carga con frecuencia. Por eso, el aceite se calienta y se desperdicia mucha energía.
En 2012, sacamos al mercado la primera punzonadora de bobina servo-eléctrica. En esta máquina, sustituimos los numerosos actuadores hidráulicos por un solo batiente eléctrico gestionado por un motor brushless, que generaba hasta 30 toneladas. De este modo, la energía que se le exigía al motor era siempre la que requería estrictamente para cortar el material.
El consumo de estas máquinas servo-eléctricas es inferior a un 73 % con respecto a las versiones hidráulicas similares y ofrecen, además, otras muchas ventajas.
El aceite hidráulico se cambia cada 2000 horas aproximadamente. En caso de filtraciones o de que se rompan los conductos, la limpieza y las reparaciones exigen mucho tiempo, sin contar con los costes de mantenimiento y de controles del sistema hidráulico.
Por el contrario, la solución servo-eléctrica solo necesita llenar de forma regular el pequeño depósito de lubrificante. Además, la máquina puede ser controlada de forma total, incluso a distancia, por el operador y el técnico de servicio.
Con respecto a la tecnología hidráulica, las soluciones servo-eléctricas ofrecen también un tiempo de ejecución aproximadamente un 22 % inferior.
La tecnología hidráulica todavía no se puede eliminar por completo de los procesos, pero nuestro servicio de investigación y desarrollo trata de extender el uso de las soluciones servo-eléctricas por las numerosas ventajas que ofrecen:
- considerable ahorro energético
- eliminación de los costes de tratamiento y de recuperación del aceite hidráulico
- Limpieza de la zona de producción
- Fácil mantenimiento y servicio a distancia
- Recorrido ajustable según necesidad
- Velocidad ajustable también en varios pasos
- Copia variable que permite proteger los troqueles
Aquí puedes ver un batiente de punzonado servo-eléctrico en funcionamiento:
Sukup, un gran productor de silos para cereales de Estados Unidos, utiliza en la actualidad seis de nuestros sistemas de punzonado a partir de bobina para realizar los componentes de chapa galvanizada, hasta un espesor de 4 mm, pasando así de los primeros sistemas de punzonado hidráulico de bobina a las últimas máquinas servo-eléctricas.
Steve Sukup explica así la inversión en los sistemas Dallan.
“ Sukup Manufacturing Co. Es el mayor productor mundial de silos para el almacenamiento de cereales, sistemas de secado, traslado y logística de los cereales, y de construcciones de acero, además de ser una empresa privada de gestión familiar. Cuando conocimos Dallan en 2008, nos gustó el hecho de que también Dallan fuera una empresa familiar y que pudiéramos hablar directamente con los propietarios.
Trabajamos grandes cantidades de chapa para fabricar nuestros productos y, en los tiempos en que conocí a Andrea, casi toda la producción se hacía de formatos. La materia prima llegaba punzonada y los productos estaban insertados en los formatos, pero siempre teníamos porcentajes de desechos muy elevados. Podían llegar al 20 o el 30 % ¡y, a veces, hasta al 60 %!
Además, había que separar y repartir las piezas, y esto suponía una gran cantidad de trabajo manual: optimizar el material era frustrante.
Entonces adquirimos la primera punzonadora de bobina, que se nos entregó en 2012. El hecho de trabajar con bobinas nos permitió reducir de inmediato los desechos a menos del 5 % y disminuir considerablemente el trabajo manual exigido, porque la producción se hace en línea y todos los componentes se separan completamente, sin microuniones. Esto también aumentó especialmente nuestra productividad, porque ya no teníamos que cargar o descargar los formatos en las máquinas: las punzonadoras de bobina “imprimen” directamente las piezas que están listas para el plegado.
Además, nuestras piezas son paramétricas: presentan formas de perforación similares en los dos extremos y a lo largo de la pieza. Muy a menudo, varía solo el largo; por eso, en la actualidad, también ahorramos tiempo en la programación de las máquinas. Solo hay que programar las diferentes configuraciones de largo y ancho en las listas de trabajo y las punzonadoras de bobina están preparadas para la producción.
De este modo, pudimos ahorrar una enorme cantidad de materia prima, tiempo de producción y tiempo de programación gracias a esta nueva tecnología y decidimos seguir invirtiendo en estas máquinas. Actualmente, disponemos de seis sistemas de punzonado de bobina Dallan y acabamos de instalar un láser Dallan para combinarlo con una de nuestras punzonadoras. ¡Así, nos hemos convertido en la primera empresa de Estados Unidos con una máquina combinada punzonadora-láser de bobina! ”
Steve Sukup
Las ventajas son tan revolucionarias que, probablemente, todavía pasará mucho tiempo antes de que sean muchas las empresas que las adquieran.
Los pioneros de este nuevo modo de producción todavía podrán disfrutar durante varios años de las ventajas de ser los primeros en cuanto a los márgenes superiores, la mejor programación y gestión de la producción –incluso con menos personal– y el ahorro de tiempo.
¿Desea conocer todas las ventajas del punzonado a partir de bobina frente al de chapa?