Sheet metal working: where is 15,9% of raw material being wasted?
In the sheet metal industry, traditional production processes start from metal sheets, with punching and laser cutting machines. The scrap generated in the process can reach 15% and more: parts nested in sheets leave a skeleton used as a support that needs to be disposed of later.
In this article, I will show how to adopt alternative and modern manufacturing technologies that start directly from metal coils, presenting a real case where one manufacturer has generated 95.200 Euro in savings per year on raw material by adopting a coil fed punch/laser production line on just 10 articles out of his production.
I will also present how to adapt the Pareto rule to identify the right articles to focus on, the industries and product types that profit from this savings, understanding the production logistic and the size of the production batches.
For more information about Dallan production systems visit coil fed punching and laser cutting lines.
Case history: Elleci Spa and the impact of raw material on production cost
The simplest way to explain how coil fed production influences the bottom line, is to show how one company has managed to profit from moving 10 articles from sheet to coil fed lines.

Elleci Spa is a manufacturer with more than 40 years experience in sheet metal fabrication: they operate in northern Italy and their manufacturing capability widens from turret punching to laser cutting systems, press brakes and panel benders, roll forming and stamping lines, coil fed punching and laser cutting lines, robot welding systems and a powder coating plant. They provide their customers 360° service including part design for manufacturing, production, assembly and packaging of the products with the original customer’s wrapping.
The following data is courtesy of Elleci company, taken from the payback calculation for the investment in a coil fed punching and laser cutting line.
First of all, Elleci selected the articles which, for their annual quantities, would easily fit into a coil fed line. Here is a selection of the 10 codes and the annual quantities produced in one shift.
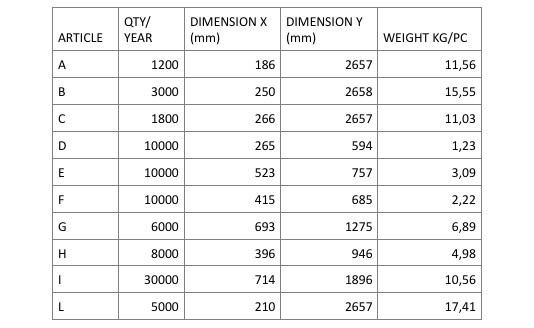
As a second step, they analyzed how many parts are fitting into a standard size sheet.
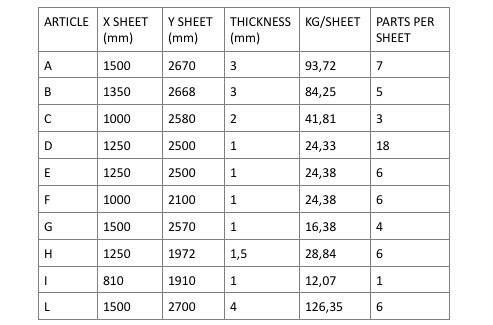
Consequently, Elleci derived the amount of scrap for each article. Elleci processes coils with the exact width of the part, therefore the amount of scrap is 2 to 3%. The following picture explains how material is optimized in a standard size sheet and in a cut to width coil.
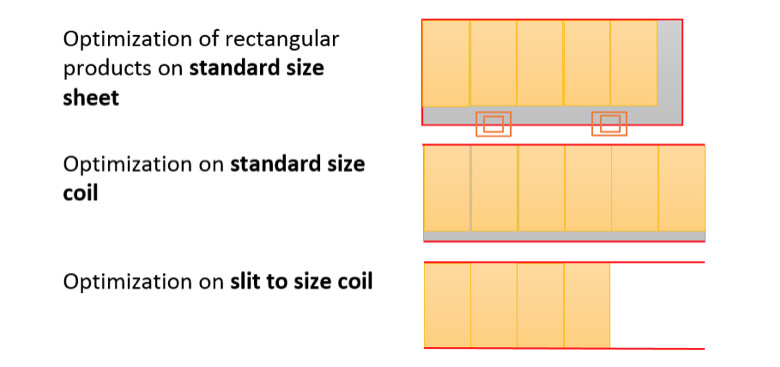
In the production of a rectangular product, on a standard size sheet the parts are nested on the surface of the metal sheet. However their positioning must take into account constraints due to the position of the grippers, and the material optimization is function of the sheet and product size.
When we work from standard size coil, we suddenly have the possibility to optimize the length to fit an exact number of rectangles.
The maximum material optimization happens in the third case, where the panels are fit into a coil that is slit to the exact size of the panel.
Comparison table
In Elleci case, the articles produced from sheet have the following percentage of scrap:
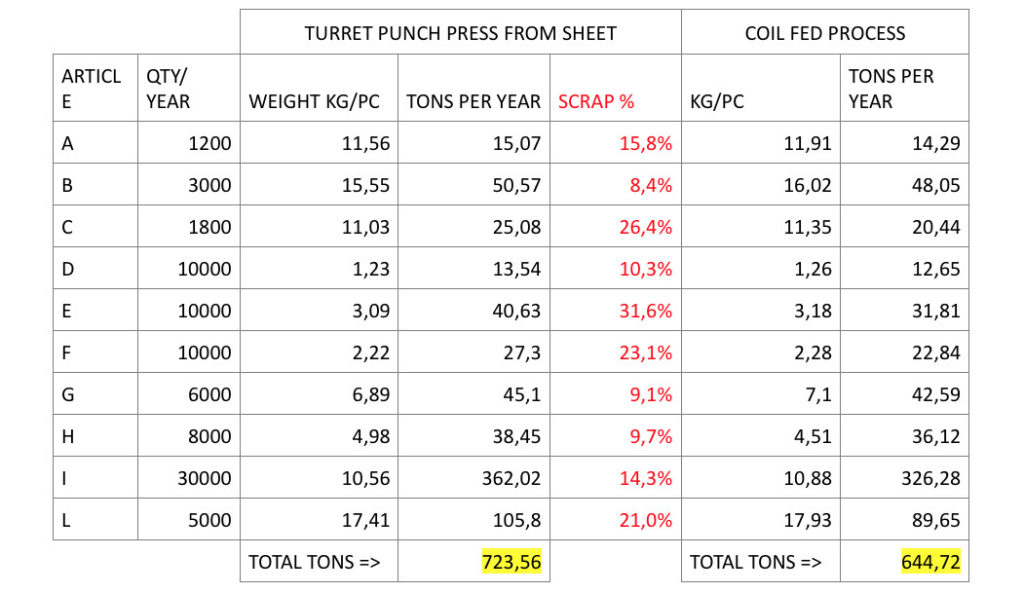
In average, in the production of these 10 codes from sheet the scrap is15,9%. The following table presents the scrap percentage per each article.
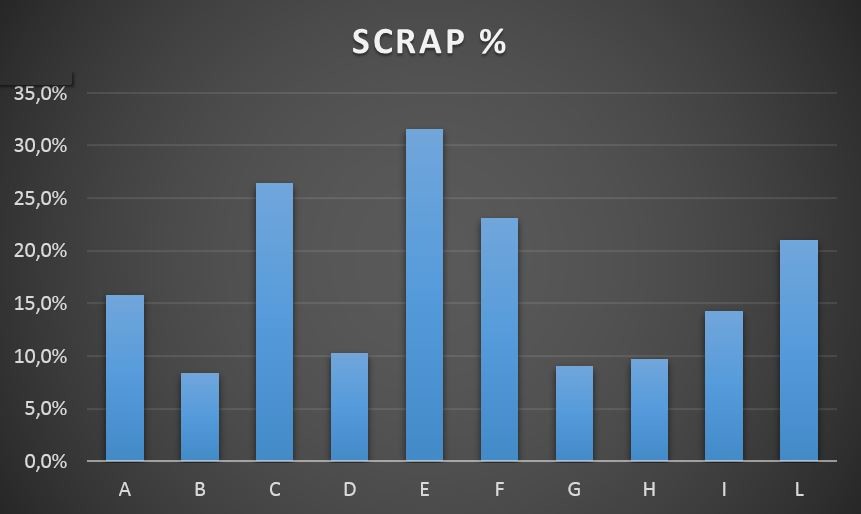
In the coil fed production, Elleci has a tiny 2 to 3% scrap: as a result, the saving in material is equal to 78,8 tons in one shift, corresponding to 47600 Euro. Having the machine to work on two shifts, Elleci has a total gain of 95.200 Euro per year just from the saving in raw material.
The Pareto 80/20 rule
In this specific case, Elleci has different technologies in its workshop to run the production: turret punch presses, laser cutting systems, coil fed punching and coil fed punch/laser lines.
In deciding which product to run from coil, it is important to look for the articles with higher production runs and the right geometry.
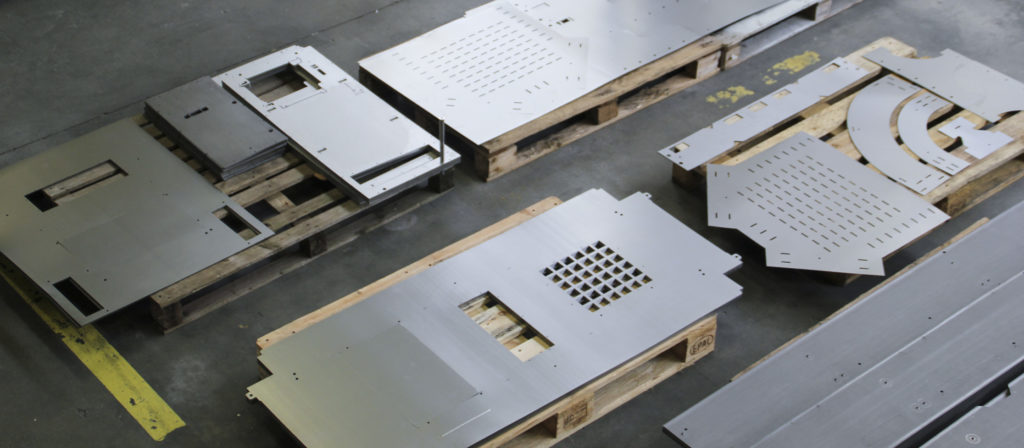
It is possible to apply the 80/20 rule to sheet metal manufacturing: “there is a 20% of the articles that uses 80% of the sheet metal processed in the workshop”. These are the articles to focus on, to consider moving them to a coil production line.
The remaining 80% of the articles uses just the 20% of the sheet metal: these are parts with smaller production runs, lower quantities and higher variability where working from sheets is preferable.
Coil fed production systems: OEMs’ great opportunity
Elleci is a sheet metal manufacturing job shop with medium to large production runs: in fact, its activity resembles more an OEM than a job shop.
In fact, the companies that most can profit of the advantages of the high productivity and material savings of coil fed lines are OEMs: thanks to their higher specialization, it is possible to focus and drive the 80% of the production directly from coil.
The size of the batches is also important. When working on a proprietary product line, it is possible to have a production organized in batches over 400-500 parts: in this way it is possible to process coils completely – the most efficient way to work with coil fed production systems.
In some cases, the production can be turned to 100% coil fed; in other cases sheet fed lines and coil fed lines complete each other to take care of the different batches sizes.
Conclusions
Today’s metal forming industry is bound to look for optimization in every aspect of its activity. Lean production leads us to identify waste and reduce it as much as possible, whether it’s in the form of WIP, inefficient processes and information flow, or useless and redundant procedures that do not generate value for the customer.
Traditional punching and laser cutting machines generate a percentage of scrap that can reach 15% and more, while coil fed lines work with just 2 to 3% scrap. Having the possibility to avoid that 15% of waste is an opportunity modern companies cannot afford to miss.
Sheet metal manufacturers and OEMs in particular have a great advantage: by analyzing their articles and quantities with the Pareto rule, it is possible to identify immediately the articles to move to coil fed production. These articles use up to 80% of the raw material and therefore the in line production from coil generates the highest savings.
In my follow up article, I will show how Elleci is gaining over 196000 Euro per year, thanks to the savings in raw materials combined with the high production speed of the coil punch/laser system.
Credits: I want to thank Giorgio Tomasella (Elleci general manager) for sharing and authorizing the use of the information presented in this article